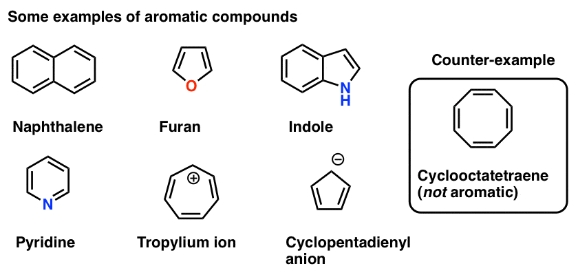
Using Crops To Produce Sustainable Plastics
When we think of oil, we think primarily of fuel for cars, ships, and planes. But petrochemicals, of which a large portion are plastics or components to produce plastics, represent 12% of global oil demand.
İçindekiler
While oil consumption is often viewed as a pollutant due to carbon emissions, microplastics are a growing concern as well. Plastic production from oil contributes to emitting both carbon and microplastics.
So, it is good news that more sustainable plastic materials are now on the horizon.
Researchers from Switzerland’s Ecole Polytechnique Federale de Lausanne (EPFL), the University of Applied Sciences and Arts of Western Switzerland, and the University of Manchester, have developed a source for sustainable plastics from agricultural wastes.
More precisely, they created sustainable polyamides using a sugar core derived from agricultural waste.
Why Polyamides?
Many plastic products, like nylons, a subclass of polyamides, need to be very durable. For this, they rely on a specific chemical structure called an aromatic group.
These aromatic groups give plastic hardness, strength, and high-temperature resistance. However, they are also often what make plastics non-biodegradable and toxic to the environment.
Source: Master Organic Chemistry
A polyamide that uses organic sugar instead of an aromatic compound would be much less toxic. The EPFL’s polyamide’s use of such sugar, which comes from agricultural waste, increases the sustainability aspect of their discovery even more.
A New Type Of Plastic
They developed a catalyst-free process to convert dimethyl glyoxylate xylose, a stabilized sugar made directly from biomass such as wood or corn cobs, into high-quality polyamides. The process relies on a series of steps, starting with the material being warmed at 140°C and then 250–260 °C.

Source: Nature.com
The process was also remarkably efficient, with a 97% atom efficiency, meaning that almost all the initial material was converted into polyamides.
The resulting material was tested to check its chemical and physical properties.
It proved to be as much, if not more, resistant to heat than traditional fossil fuel-based polyamides. It also performed well in durability and mechanical resistance (tensile strength).

Source: Nature.com
One limitation the researchers found is that the material might be sensitive to exposure to large amounts of water, so it could not be submerged. It might also be too permeable to oxygen and water to be used in thin food packaging. Importantly, plenty of possible applications remain.
Sustainable Plastics Ready For Industrial Use
Usability
Another factor to take into account for industrial applications is “processability.” Or the ease of turning the raw plastic base components into useful materials.
The researchers demonstrated that their new material can be used for piston injection molding and high-shear twin-screw extrusion, which are both common methods for shaping plastics.

Source: EPFL
They even tested its properties for 3D printing, using high-temperature settings to produce an iPhone 11 case successfully.

Source: EPFL
Recycling
Another test was to check the potential for recycling of the new polyamide material. They re-used the plastic through high-shear twin-screw extrusion 3 times.
The tensile properties remained nearly identical across the three cycles.
The coloration increased slightly at each cycle. However, if needed, the orange color can be avoided entirely by tweaking the production process (improved purification of diamines), so this would not be a major issue.
Overall, mechanical recycling showed good performance, which was equal or superior to existing plastic supplies.
Finally, they also investigated the possibility of chemical recycling as an end-of-life option for plastic. This relied heavily on powerful acids like sulfuric acid but demonstrated that it could be fully recycled with chemicals at the end.
A Cost-Competitive Alternative
For the industry to adopt such sustainable plastic (without regulation changes), it will need to be cost-competitive against established fossil fuel-based chemicals.
The price of nylon 66, the most common polyamide, is usually between $3,000-7,000/ton. The prices of the new material would be in a similar range, even when assuming relatively high costs for the source material.
Potentially, using materials from cheaper sources like corn cobs could make it even cheaper.

Source: Nature.com
In addition to being price competitive, the new material is a much smaller emitter of carbon and greenhouse gases than the existing products on the market, especially if using xylose from corn cobs instead of commercial xylose.
Sustainable Plastics – A Needed Advancement
New types of bio-plastics, as in this study, are needed to reduce the consumption of fossil fuels.
This represents a new step, where a new type of plastic molecules with similar or superior performances are created instead of trying to recreate traditional plastic chemicals with a biomaterial source.
Most likely, replacing aromatic groups from fossil fuels with biological sugars is just the beginning.
This approach is more difficult but also allows for new plastic supplies that display many advantages compared to traditional ones:
- Lower carbon footprint.
- Less pollution.
- Valorization of agricultural waste products.
- Potential decline in costs or improved chemical properties.
The success of the EPFL team (and its research partners) should be used as a template for other innovations in using biomaterials to create new useful industrial chemicals instead of just trying to replicate exactly the existing plastics using chemical structures abundant in oil.