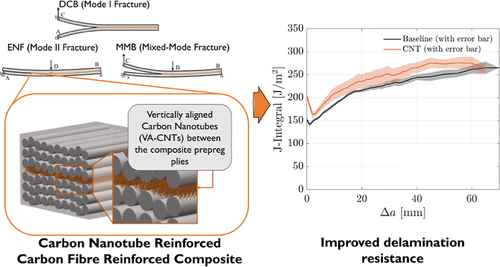
A study published in the scientific journal ACS Applied Materials and Interfaces introduces an innovative method for binding composite material together called nano-stitching. This process combines thin-ply carbon fiber laminates to create a velcro-like bond between layers. The result is a more durable and lightweight material that can withstand extreme environments. Here’s what you need to know about nano stitching and how it could change the world you live in.
İçindekiler
What is Nano Stitching?
Nano stitching is a process of binding composite layers together using lab-grown vertically aligned carbon tubes. These hollow tubes are created using a special chemical vapor deposition process. This vapor reacts with other catalysts during the baking process.
The carbon falls to the surface as a microscopic forest of nanotubes. These microscopic tubes can result in billions of bindings when sandwiched between layers of thin-ply carbon fiber laminate. These thin layers are only around 50 micrometers in width. This thickness is a 3rd of a hair for comparison.
- Nanostitching – ACS Applied Materials & Interfaces
The thin forest binds to itself like velcro to create a uniform and durable connection. This added strength could have implications across multiple industries. As such, any industry that uses composites could benefit from the technology and leverage it to retain structural integrity.
Problems that Nanostitching Helps Solve
There are many issues that nano stitching could help to alleviate. For example, composite materials can often have microscopic cracks within their layers that are hard to find. These cracks can suddenly expand and cause layers to separate or shatter.
Nano Stitching replaces the current method of gluing the layers together. Since it has so many uniform points of contact, tears, rips, and cracks don’t spread as easily compared to a layer of dried glue. As such, nano sticks could have a massive impact on the durability and weight of future composites.
Delamination
Delamination is a term that refers to the potential for composite layers to separate. Delamination is a serious concern when you have multiple materials connected via adhesives. Each layer adds a little more chance of delamination in the current process. Nano stitching provides a more resilient and durable solution for manufacturers.
Hard to Inspect
It can be difficult to detect internal damage to composite materials. Each layer adds another complexity to the process. Additionally, a single composite could react differently than other layers under different conditions. When this occurs, there can be no outward signs.
Nanotubes add interlaminar strength via billions of points of contact. This process could help reduce the need to detect these cracks as they wouldn’t spread or fail spectacularly. They could be located and repaired safely using nano stitching to mend any repairs.
Structural Weaknesses
Every structure has points that are weaker than others. Engineers see nano stitching as the ideal way to reinforce key points of their creations. Imagine nano-stitched composite used around bolts or heavy load areas. The lightweight support could one day make buildings safer.
Manufacturing Processes
The current way of binding composite layers is inefficient. Eliminating the use of adhesives and instead binding these layers on a molecular level is a better option that provides reliable results. Additionally, the process is easier to accomplish versus using adhesives to bind layers.
MIT Engineers
MIT Engineers were behind this advantageous project. The team included Carolina Furtado ,Reed Kopp, Xinchen Ni, Carlos Sarrado, Estelle Kalfon-Cohen, and Pedro Camanho. It was led by Professor of Aeronautics and Astronautics Brian Wardle. Notably, Wardle is the director of Necstlab which specializes in composite materials.
Testing
The research paper goes into detail regarding the testing process and results. The testing phase was led by Carolina Furtado. Furtado is an expert in the field and has helped create advanced models to mitigate cracking.
The test was conducted on an advanced composite that measured only 3 millimeters thick. Impressively, the researchers nano-stitched 60 layers of polymer sheets to test crack resilience.
The first test began with engineers creating a crack where the layers met on the edge. They then measured the resistance and breaking points. The delamination test checked the resilience of the bond between layers. They found that the cracks did not spread and the layer remained held tight.
Potential Applications Nano Stitching Applications
There are many use-case scenarios where nano stitching could have an immediate impact. The number of industries and goods that use composite materials continues to expand. As such, there’s a demand for lighter more resilient options. Here are some of the industries that nano stitching could upend shortly.
Aerospace
The aerospace industry has a lot to gain from the improvement of composite. These materials have become one of the main ways manufacturers cut weight and improve durability. Some composites can reflect radar waves and more.
Nano stitching would enable manufacturers to create high-value aerospace structures. These planes of the future will be lighter and run on advanced engines. They will leverage the strongest and lightest materials to help improve battery life and durability.
Architecture.
Nano-stitching opens the door for better buildings and infrastructure. Imagine 3D-printed homes that can withstand the harsh weather. The use of composite materials in building advanced structures like bridges could help make travel safer for everyone.
Automotive.
Electric cars are here but one of their biggest drawbacks is battery life. Reducing their weight would help to expand their battery life further and make EVs more attractive to more clients. Already, firms like TESLA integrate composite to help improve durability and improve manufacturing processes.
Energy Production and Storage
Nano Stitching will make power generation more efficient. Imagine lightweight windmills or solar panels that could withstand more damage before failure. They would be easier to set up and could handle more load than the current models which would result in better efficiency and availability.
Marine Engineering
Underwater exploration is another industry that has long worked with composites to help create the most efficient underwater designs. Nano stitching could help humans go deeper than ever before by enabling engineers to make underwater structures that could withstand the massive pressure at the depths of the ocean.
Robotics
The robotics industry is always in search of the lightest, most durable materials. The integration of nano-stitched composites could make robots lighter and travel farther. It could also help advanced robotics become more portable and available to the global market.
The field of biohybrid robots could see a boost from these lightweight composites. These robots leverage organic materials merged with lightweight and often micro components. Nano stitching would provide a durable way to bind tiny robot components.
Companies that Could Benefit from Nano Stitching
Many companies could increase revenue and product enhancements thanks to nano stitching. These firms span industries from healthcare to military applications. Here are a few companies that could see an immediate boost if they integrate nano stitching into their business models.
Owens Corning 
Owens Corning is the largest manufacturer of fiberglass composites in the world. This Ohio-based firm was founded in 1935 and went public in 1955. In 1985, the company expanded its market position after acquiring Aerospace and Strategic Metals Group. Today, Owens Corning has +30 composite facilities.
Owens Corning could use nano stitching to boost its foray into the aerospace market. They could provide more resilient components and further their positioning. Additionally, they could further research what materials nano stitching holds tightly.
Teijin Limited
Teijin Limited is a Japan-based manufacturer that specializes in the creation of composites, resins, plastics, and fibers. The firm has been in operation since 1918 and remains a pioneer in the composite market. Currently, the company has +20k employees across 20 countries of operation.
Nano Stitching makes sense for Teijin as it would improve many of their products. The firm could integrate this style of composite binding on multiple products they currently offer and lower weight and improve structural integrity.
Hexcel 
Hexcel is recognized as one of the leading manufacturers of composite materials. The company’s main product is honeycomb manufacturing which is primarily used in aerospace applications. The honeycomb structure provides reduced weight with optimal durability.
Hexcel could easily benefit from nano-stitching integration across its multiple sectors. The manufacturer already offers carbon fiber reinforcement and resin systems. Nano-stitched products would give them a competitive edge.
Nano Stitching Could Power the Next Moon Mission
The use of nano stitching to improve current and future composites could help engineers develop the next-generation spacecraft needed to reach other worlds. For now, there are plenty of on-earth use cases that make nano stitching an interesting development.
You can learn more about cool manufacturing projects here.